In manufacturing, operational executives play a critical role in overseeing and managing the overall, aggregated day-to-day operations. However, in the dynamic nature of manufacturing, it’s easy to get caught up in looking for high-level trends and optimization opportunities to improve overall profitability, when the real insights are often in the granular details. In this blog, we will explain why developing a data-driven bottom-up approach to understanding cost drivers in operations can lead you to unexpected insights to improve profitability.
How to determine the cost drivers in your value chain
Understanding cost drivers
At the heart of cost management is a simple yet powerful concept: cost drivers. These are the gears and levers that directly influence the cost of an activity and set the stage for your organization’s financial performance. But more than just line items on a balance sheet, cost drivers are the key to unlocking deeper insights into the underlying forces that shape your bottom line.
Cost drivers aren’t just arbitrary numbers-they’re the building blocks of cost behavior. Think of them as the DNA of your business, governing how costs rise and fall in response to changes in business activity or production volume. By understanding the causal relationship between cost drivers and spending, you gain the ability to predict how changes in those drivers will affect overall costs. A critical capability in the quest for cost reduction and operational efficiency.
Unpacking cost drivers in operations
Enter Michael Porter and his important work on competitive advantage. Porter introduced a systematic way to analyze a company’s activities through the lens of the value chain. This framework divides activities into two main categories: primary activities and support activities and provides a roadmap for understanding where value is created and where costs are incurred (Figure 1).
Let’s bring this theory down to earth with a practical example. Let’s say you’re looking to reduce costs at the operational level of your value chain. What are the key cost drivers you need to consider?
- Labor costs: Direct labor hours and labor rates are obvious candidates. After all, labor is often one of the largest expenses in manufacturing operations.
- Raw materials: From price to volume, every aspect of raw material procurement and usage plays a role in your costs. Quality control and waste management are also critical factors to consider.
- Equipment: Total machine utilization, depreciation, maintenance, and downtime all contribute to the cost equation. Maximizing the efficiency and life of your equipment can result in significant cost savings over time.
- Energy: In an era of rising energy costs and environmental awareness, monitoring power usage and managing peak usage can make a significant dent in your operating costs.
In manufacturing, understanding cost drivers is not just a nicety – it is a necessity. By analyzing the various factors that influence costs at each level of your value chain, you gain the insight you need to make informed decisions and drive meaningful change.
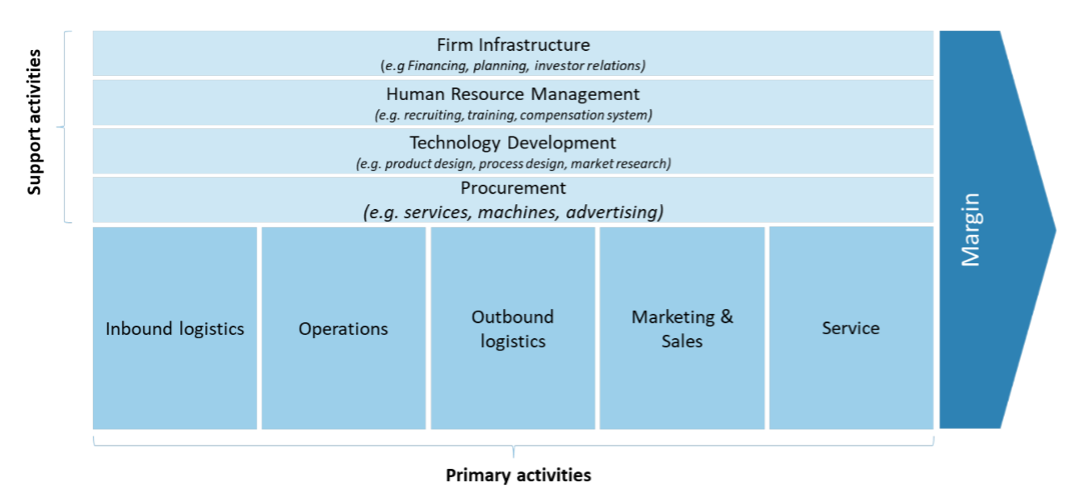
Â